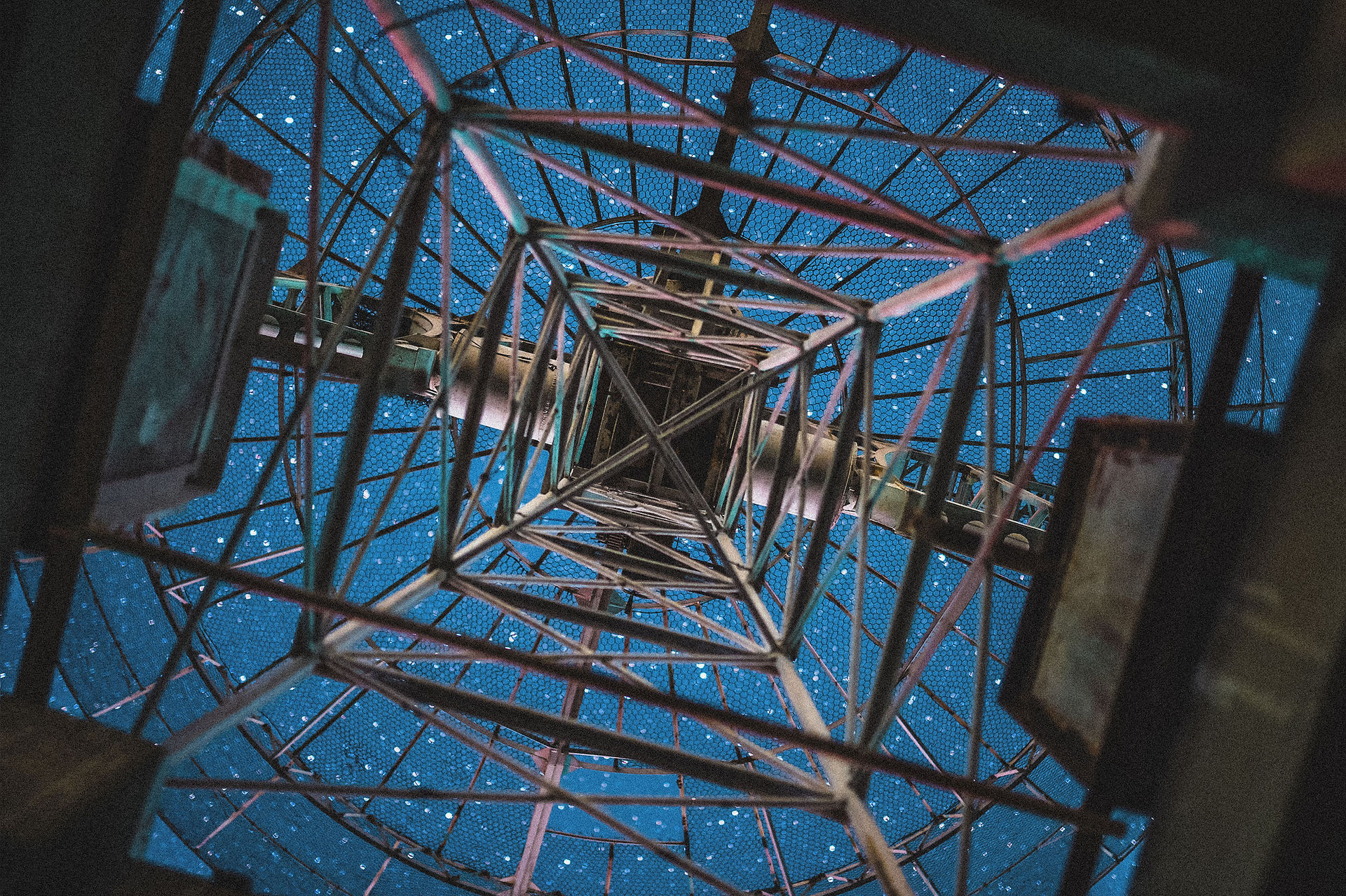
Frequently Asked Questions
What is the advantage of piezoactuators over other actuators?
Piezoactuators are wonderful choice for small precise movements. Their high output force makes them more suitable for heavier loads compared to electromagnetic actuators. They can maintain their position for a long time without drawing too much current so they can be used for precise alignment.
What is the advantage of piezoelectric actuators over voice coils?
Piezoelectric devices can provide higher forces in much smaller distances, that makes them better for manipulating large loads at higher frequencies. Because of the higher electrical time constant of the voice coils, they cannot response as fast as piezoelectric actuators. Also, they can stay at the same position for a long time without consuming much power. Voice coils need constant current to keep a static load at the same position.
How can I select the right piezoactuator for my project?
In order to select the right piezoactuator, you need to determine how much free stroke and blocked force you need. The free stroke of a piezoactuator refers to the maximum displacement or movement it can achieve when it is not subjected to any external load or resistance. Blocked force is, on the other hand, the maximum force the actuator can exert when its motion is fully constrained. Under loads exerting constant force on the piezo (such as lifting an object against gravity), you can get displacements near free stroke. If your load force varies over time or position, load stiffness and dynamic forces should be taken into account and more detailed analysis should be done.
Is stiffness of the piezoactuator important?
Stiffness of the actuator is especially important when you need dynamic operations. The resonance frequency, response time and stability of the system depends on the actuator stiffness and load inertia. As your load inertia or working frequency increases, or you need faster responses, you need higher stiffness.
How hot a piezoactuator can get?
In small signal operations, piezoactuators have a loss factor (ratio of the dissipated heat vs electrical energy needed to fill the piezoactuator's effective capacitor) around 1-2%. But when are operating at their full range, the loss factor can go more than 15% and that causes high amount of heat dissipation during high frequency operations. Large piezoactuators have less surface area compared to their volume so additional cooling could be needed for adequate cooling. Otherwise you can get up to 80 C temperature rise.
Can I attach my own mirror on your FSM?
Yes, you can definitely attach any mirror on FSM but the performance characteristics could be different. The resonance frequency and bandwidth is related to the rotational inertia of the mirror. Mirrors with larger intertia should operate at lower frequencies.
What is flexure guide?
Flexure guide is flexible members of the mechanical structure that allow movement in desired direction but resist movement in other directions. They eliminate the need of rolling and frictional bearing elements. Using flexure guides eliminates backlash, slip-stick forces and part count. They also provide vacuum and cryogenic compatibility since they eliminate the need of lubrication. They can maintain nanometer level precision for a long time because they eliminate wear.
What are the advantages and disadvantages of strain gauges?
Strain gauges are thin strips that changes resistance with deformation. By measuring this resistance change, you can detect displacements with sub-nanometer resolution. They are compact and cost-effective compared to other precision sensors.
The main disadvantage of the strain gauges are their limited range. Their range is mostly determined by the deformation limit of the substrate material. They also need proper technique for bonding to ensure accurate measurements. After that, their output signal need sophisticated amplification circuits. Despite these challenges, they are often the best option for precision motion systems.
Why do you need Fast Steering Mirrors?
Fast steering mirrors are used for manipulating light beams' direction at high frequencies (100s Hz or even 1000s Hz) with small amplitudes, usually around several milliradians. There are several applications: laser beam stabilization, optical image stabilization, laser beam scanning and tracking, dithering micro scan, backscanning.